نوقشت رسالة الماجستير للطالبة غدق محمد عباس / قسم هندسة التصنيع المؤتمت الموسومة:
( Optimum parameters selection for metal cutting of composite material in milling machine )
وبأشراف أ.د. فتحي عبد الصاحب عبد الحسين / قسم هندسة ميكانيك / كلية الهندسة / جامعة بغداد ( مشرف أول ) و م.د ايناس عبد الكريم / قسم هندسة التصنيع المؤتمت / كلية الهندســــة الخوارزمـــــــي / جامعة بغداد (مشرف ثاني) .
حيث حصلت الرسالة على درجة تقدير (مستوفى) وكانت اللجنة العلمية للمناقشــــــة برئاســـة أ.د شكري حميد غضيب / قسم هندسة الانتاج والمعادن / الجامعة التكنولوجيــة وعضويــة أ.م.د علي حسين كاظم / قسم هندسة التصنيع المؤتمت / كلية هندسة الخوارزمـــــــي / جامعة بغداد وعضويــة م.د صلاح سلمان عبد الكريم / قسم هندسة التصنيع المؤتمت / كلية هندسة الخوارزمـــــــي / جامعة بغداد .
ملخص البحث هو في السنوات الأخيرة ، تم استخدام المواد المركبة على نطاق واسع في تطبيقات مختلفة نظرًا لوزنها الخفيف وخصائصها الحرارية والميكانيكية الجيدة , هذه الدراسة هي محاولة لتطوير معايير التصنيع المثلى وتقييم تأثير ذلك على القطع المعدني للمادة المركبة في التحليل النظري ، يتم استخدام طرق متعددة لتصنيع أنواع مختلفة من المركبات, يعُد التشكيل اليدوي طريقة قديمة ، لكنها لا تزال مستخدمة حتى يومنا هذا نظرًا لمرونة اختيار الألياف والمعادن والبوليمر ، كما أنها أسهل في تصنيع العديد من المواد المركبة نظرًا لبساطتها. المتغيرات المحددة هي سرعة القطع للعملية ، ومعدل التغذية ، وكذلك عمق القطع في المادة المركبة ، والتي يمكن محاكاتها من طريقة الطاقة باستخدام برمجة MATLAB 13 لحل المشكلة لأنواع مختلفة من الألياف. في التجارب ، تم تطبيق طريقة تاجوشي. تم اختيار المصفوفات المتعامدة L9 ونسبة الإشارة إلى الضوضاء) S / N( وتحليل التباين )ANOVA( لتحسين المتغيرات. تم التحقيق في تحديد وتحليل تأثير متغيرات التحسين باستخدام برنامج .MINITAB في التحليل العملي ، تم استخدام طريقتين لتصنيع المركبات لهذه الدراسة ؛ الطريقة الأولى هي طريقة الضغط ، والتي تتم عن طريق الضغط على العينات في القالب لمدة 10 ساعات. الطريقة الثانية هي طريقة التسخين. يمكن أن يتم ذلك عن طريق وضع العينات في قالبها في الفرن لمدة 12 ساعة تقريباً مع درجات حرارة محددة. يستخدم نوعان من الألياف: الألياف الزجاجية – الألمنيوم والألياف الكربونية – الألمنيوم. كانت أبعاد العينات 100 ملم × 100 ملم × 2.8 ملم. كانت أنواع مختلفة من المركبات تم تصنيعها لأختبار تأثير ثلاث متغيرات على خشونة السطح باستخدام ماكينة القطع المبرمج) CNC(. اتجاهات ألياف الكربون المستخدمة في المركبات هي ± 45 درجة ، ± 60 درجة. النسبة الوزنية للألياف 38٪ والبوليمر 34٪ والألمنيوم 28٪. كان التحدي هو كيفية تصنيع مادة مركبة بواسطة التشكيل اليدوي تتكون من الألياف والبوليمر وسبائك الألومنيوم 6061 بدون حصول تفكك وتماسك جيد بين المعدن والألياف. يعد تصنيع المواد المركبة من الصفائح أمرًا ضرورياً للعامل سواء في الوقت المناسب أو خشونة السطح. يجب تقليل هذين العاملين مع الحفاظ على جودة المركب ، للحصول على شكل نهائي أفضل ومفيد في التطبيقات. تؤكد النتائج أن أفضل متغيرات المركبات في طريقة الضغط للألياف الزجاجية – الألمنيوم مع البوليستر كمادة رابطة هي سرعة المغزل 5000 دورة في الدقيقة ، وتغذية 1600 ملم / دقيقة والعمق 1.6 ملم ، والألياف الكربونية – الألومنيوم مع البوليستر هي 4000 دورة في الدقيقة سرعة القطع ، 1600 ملم / معدل التغذية بالدقيقة ، وعمق القطع 1.2 ملم. بالنسبة لطريقة التسخين ، فإن المتغيرات ليست مؤثرة كما في طريقة الضغط. النتائج والمقاييس المثلى للألياف الزجاجية – الألومنيوم والألياف الكربونية – الألومنيوم مع الايبوكسي هي سرعة القطع والتغذية وعمق القطع ، 3000 دورة في الدقيقة ، 1200 ملم / دقيقة ، 1.2 ملم و 5000 دورة في الدقيقة ، 1600 ملم / دقيقة ، 2.0 ملم ، على التوالي.
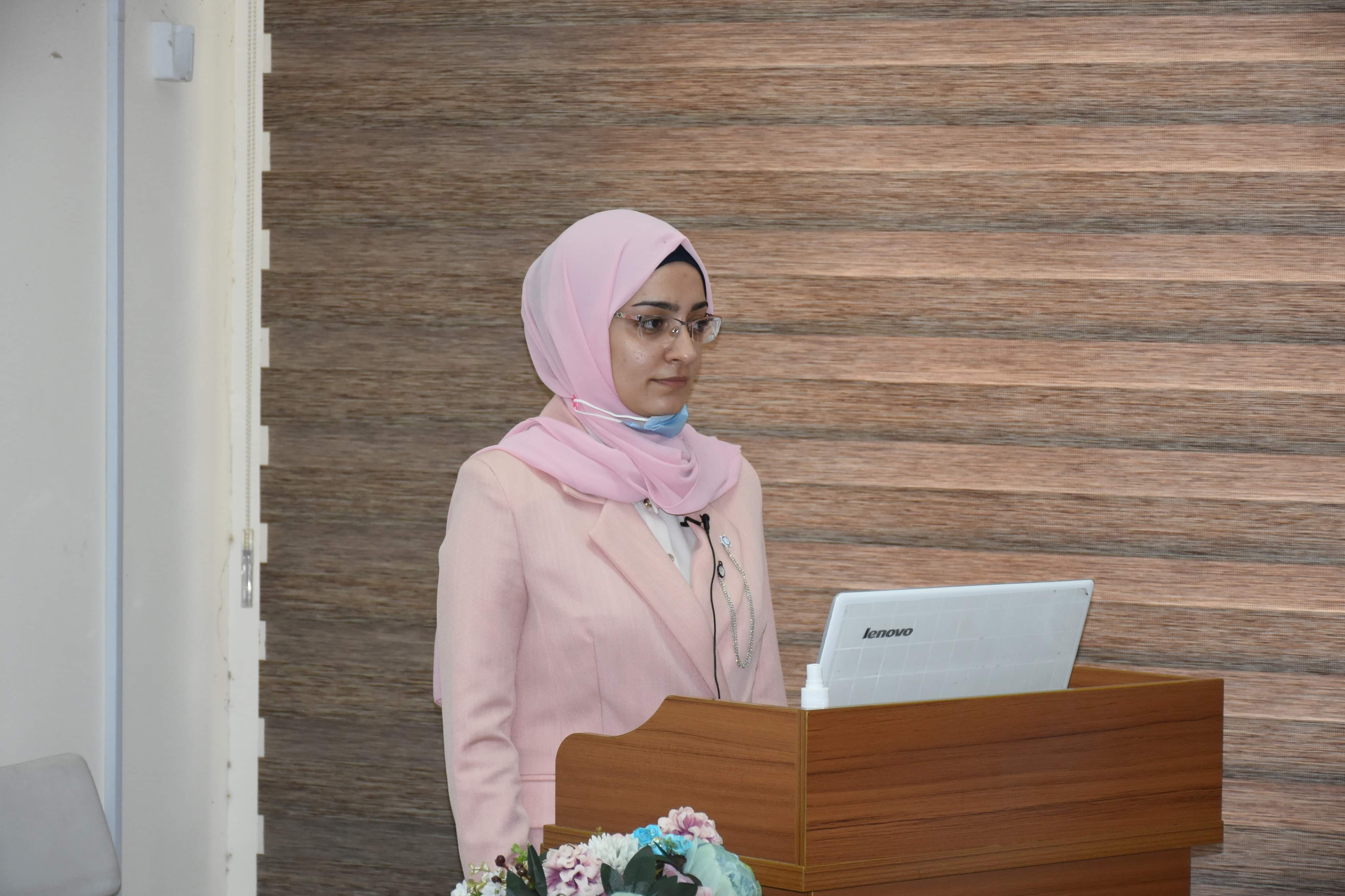
Comments are disabled.